Home / HSSE
HSSE
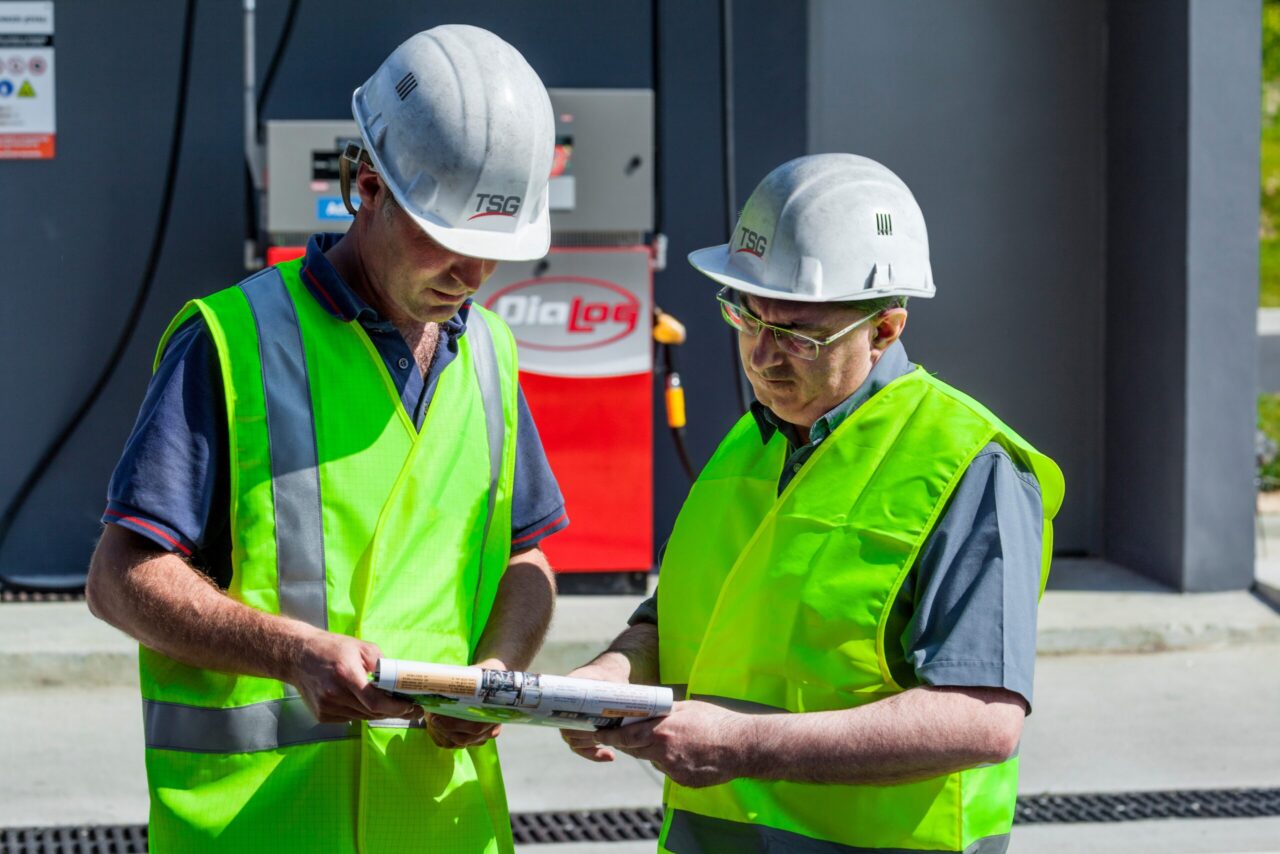
HSSE is a fundamental part of our business. Our management teams, at all levels, are directly involved in the development of HSSE objectives at an individual and organisational level. We use a common set of rules, guidelines and reporting tools to help ensure a high level of professionalism and adherence to both local and global standards wherever we operate. We have a strict selection policy and training programmes for all our contractors. Our goal for ‘zero accidents’ aims to ensure a safer environment for our staff, our clients and their end-users.
We have won many awards from customers across the globe for our commitment to ensuring a safer environment for our staff and our customers. Recent awards received by include:
Our global and local HSSE teams work closely with each other to share best-practice, pro-active safety initiatives and ‘lessons learned’ from accidents, incidents and Near-Miss reports. All of this is vital to allow us to achieve our goal that everyone returns home safe every single day.
Our safety culture is embedded across all our divisions. Based on the strategic company goal of “Zero Accidents”, the TSG philosophy is that no accident is acceptable, and that investigation, root cause and learnings from accidents are at the heart of positive change. Our HSSE community ensure this belief is used to understand and share important safety information.
Near-Miss reporting lies at the heart of our proactive approach to safety management, with employees submitting reports of near-misses and potential hazards. These reports are shared with our customers in order for them to take action to rectify defects on their own premises and are also reported internally for logging and analysis. Expanding the use and ability of our service database, Kimoce, has allowed us to ensure local reports can be accessed, downloaded and submitted to clients expeditiously. This allows for better trend analysis and prompts global action on common issues.